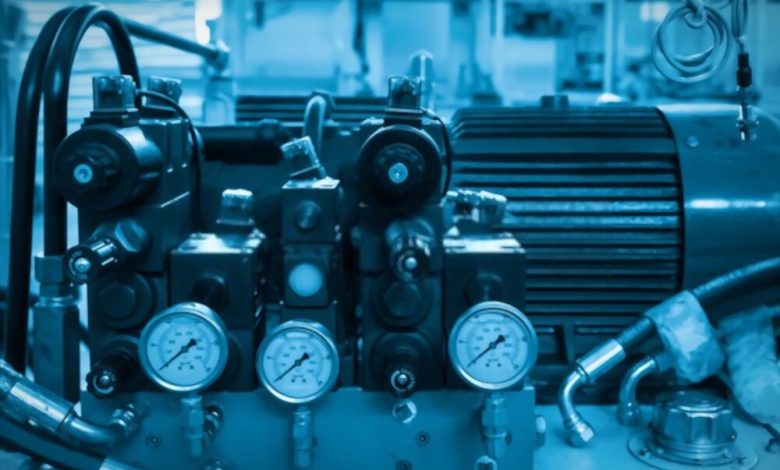
A Hydraulic System is made up of many components. A complete drawing of a hydraulic circuit contains components, their descriptions, the sequence of operations, and notes. A hydraulic-circuit diagram is an indispensable tool for hydraulic system builders and designers. It shows all the different components, how they work together, and how to connect them so that the entire system will operate smoothly. This article will cover all of these components in detail.
Flow control valve
These parts all act to regulate the flow of the fluid and are classified according to their purpose. For example, the controlled flow port controls the flow rate of a fluid while the excess flow port allows all of the fluid to pass through. Both types of valves are useful in different applications.
Non-pressure-compensated flow control valves offer a constant volume flow rate, while pressure-compensated valves are used for variable-rate applications. In addition to controlling flow rate, they are also useful for keeping the cylinder at a constant speed. The volume flow rate of hydraulic fluid is directly proportional to the speed of the hydraulic cylinder. By regulating the flow rate, pressure-compensated flow control valves make it possible for a hydraulic cylinder to operate at a consistent speed.
Fixed-orifice flow control valves are the simplest types of flow controls. In other words, these valves simply have an orifice or a calibrated needle that is open and closed. If a part of the orifice is obstructed, flow will be reduced. Other more sophisticated types of flow control valves monitor and sense pressure fluctuations and flow rate. Pressure-compensated variable flow valves have a range of accuracy, usually within 3% to 5%. They also have the advantage of being temperature-compensated, allowing them to compensate for viscosity variations.
Solenoid valve
A solenoid valve is an electromagnet that encircles a solid metal core. Because of its small volume and relatively high magnetic forces, solenoid valves can have extremely fast response times. The following are some characteristics of solenoid valves, which can affect their performance. Response time: The amount of time between the switching signal and the valve’s mechanical opening. The cycle period: The total time between energizing and de-energizing a solenoid valve. The preferred cycle period is either 2, 5, or 10 minutes. Relative duty cycle: When a valve is in continuous operation, it is operating until its internal temperature reaches a steady state.
This action is accompanied by an increase in the volume of the oil within the valve chamber. Once this happens, the actuator moves toward the oil port B. Solenoid valves can be classified into three different types: two-way valves, three-way valves, and directional valves.
Another type of hydraulic valve is a pressure relief valve. These valves open when the pressure in the hydraulic system reaches a certain maximum level. They divert the pump flow back to the tank or reservoir.
A hydraulic solenoid valve is a directional valve that opens and closes a hydraulic system. Its solenoid controls the flow of fluid and is controlled by an electrical current. A hydraulic solenoid valve consists of a cylindrical spool with grooves. The spool blocks the flow while the land allows it to pass through.
Pump
One of the most common hydraulic system components is the pump. Pumps deliver fluid to a variety of devices, from hydraulic jacks to water pumps, and many other products rely on them for movement. A pump’s primary purpose is to move fluid. When working properly, it allows the fluid to travel through the pipe system without any friction or pressure. Its inlet and return valves are connected to a hydraulic reservoir.
A hydraulic system also includes a reservoir that stores fluid and protects it from contamination. The pump enables fluid to move and transmit force, and also displaces air. There are different types of hydraulic pumps, each designed for a specific environment and operating conditions. Using the wrong one can result in operational problems and system failure. This article covers some of the most common types of hydraulic pumps and their various components.
A hydraulic system uses pressurized hydraulic fluid to drive connected equipment. Hydraulic systems are found in a variety of applications and devices, from cars and construction sites to the manufacturing industry. They can move massive loads and travel at high speeds, which makes them extremely useful in many settings. It can even power a car. These systems are everywhere. The pumps power everything from cars to cranes.
Most hydraulic systems share components and parts. They contain a reservoir for the hydraulic fluid. In order to maintain the best functioning of the hydraulic system, owners should perform regular inspections of the hydraulic system. When it’s time to replace the pump, make sure to refer to the manufacturer’s manual for the proper procedure for replacing or cleaning the hydraulic pump.
Click here to read more:https://www.swseal.com/Hydraulic-System-Components
Reservoir
A hydraulic system consists of several basic components including the reservoir, pump, and piping. These components operate at varying pressures, depending on the system’s requirements. The reservoir provides space for the fluid to expand and evaporation to take place. In addition, the reservoir allows for air to escape, which helps cool the fluid. A hydraulic system also contains a reservoir for recharging fluid when necessary.
Some reservoirs feature visual gauges to indicate the quantity of fluid inside. These may be a glass tube, direct reading gauge, or float-type rod visible through a transparent dome. Quantity transmitters also allow the pilot to read the fluid quantity in the cockpit. The reservoir consists of a welded body and cover assembly clamped together.
Hydraulic systems need a pressurized reservoir to deliver fluids to the hydraulic pumps. In some cases, atmospheric pressure may be insufficient to pressurize a reservoir, so a fluid-pressurized reservoir is necessary. Pressurized hydraulic reservoirs are equipped with relief valves, and they also feature hinged tops. In addition to pressure relief valves, some hydraulic reservoirs have internal temperature gages.
The reservoir is one of the most crucial components in a hydraulic system. It stores the hydraulic fluid in the reservoir and protects it from the air. The types of pumps are gear, vane, and piston pumps. Whichever type you choose, you’ll be able to use it to move objects.
Thanks for visiting postingpall