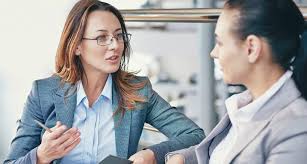
Before you start with the fundamentals of lean, you should know that lean Management aims to continually improve ways of working, goals, and people.
Rather than trying to have total control over and focusing on work methods, lean management or M&A advisory promotes shared responsibility and leadership.
Therefore, the two main pillars of the lean methodology are:
- Respect for individuals
- The amelioration keeps going
After all, a good idea or initiative can start at any level in the hierarchy, and lean trusts the individuals doing the work to know how it should be done.
Currently, lean management is a concept that is widely adopted in various industries. It stems from the Toyota Production System, which was developed around 70 years ago.
The birth of lean
In the 1940s, when Toyota laid the foundations of lean manufacturing, the goal was to minimize processes that did not add value to the final product.
In doing so, the company has managed to significantly improve productivity, efficiency, cycle time, and cost optimization.
Thanks to its notable impact, lean thinking has spread to many sectors and has evolved into the 5 fundamental principles of lean strategy described by the Lean Management Institute.
Indeed, the term “lean” was first used by John Krafcik (the current CEO of Google’s self-driving car project, Waymo) in 1988, in his article titled “Triumph of the Lean Production System”.
lean software development
In 2003, Mary and Tom Poppendieck published their book, “Lean software development: an Agile Toolkit”. The book describes how you can apply the basic principles of lean-to software development.
Ultimately, lean software development is based on 7 principles. Although at first, it did not meet with great popularity, a few years later it became one of the most widely used software development methods.
The lean start-up (what is lean in business?)
Eric Ries, an engineer, and serial entrepreneur developed a methodology based on lean principles to help start-ups succeed. In 2011, he collected his ideas in a book called “The Lean Startup”. These are 5 fundamental principles that aim to enable start-ups to be more flexible and adaptable to change.
From an entrepreneurial perspective, the goal is to shorten product development cycles and quickly discover if a business concept is viable. This methodology is also used by government structures, marketing professionals, and other actors.
As you can see, lean management is not a spontaneous creation. Rather, it is a concept that is gradually evolving, thanks to many observations and the desire of individuals to continuously improve.
Now is the time to look at the fundamentals of lean management.
The 5 fundamental principles of lean
What are all societies trying to do? Offer a product/service that a customer is willing to pay for. To do this, a company must add value defined by the needs of its customers.
The value is in the problem you are trying to solve for the customer. Specifically, in the solution your customers are willing to pay for. Any activity or process that does not add value to the final product is considered wasteful.
You must therefore start by identifying the value you want to provide before moving on to the next step.
-
Mapping the value chain
This is the step where you need to map your business workflow. This should include all actions and individuals involved in the process implemented to deliver the end product to the customer. You will be able to identify the parts of the process that add no value.
Applying the lean principle to value stream mapping will allow you to see where value is generated and how much of the different parts of the process do or do not produce value.
Once your value stream is mapped, it will be much easier for you to see which processes belong to different teams, and who is responsible for measuring, evaluating, and improving them. This overview will allow you to detect and eliminate steps that add no value.
-
Create a continuous workflow
Having a stable workflow ensures that your teams can complete assigned tasks much faster with less effort. However, to ensure the stability of the workflow, be sure to develop a method of regulating the flow.
With such a method, work is performed only if there is a demand for it. This allows you to optimize resources and only provide a product/service if a genuine need exists.
Take, for example, the case of a restaurant. You come in and order a pizza. The chef receives your order and begins to prepare your pizza. He doesn’t prepare tons of dishes in advance, because there is no effective demand for them, and they can turn into a waste of resources.
-
Design of a flow regulation method
Once you have your value chain under control, you need to ensure that each team’s workflow remains fluid. Keep in mind that this may take time.
Developing a product/service will often involve cross-functional teamwork. Bottlenecks and interruptions can appear at any time. However, by breaking the job into smaller chunks and visualizing the workflow, you can easily spot and remove roadblocks.
-
Continuous improvement
After all the previous steps, you have already built your lean management system. However, do not forget to pay attention to this last phase, probably the most important.
Remember that your system is neither isolated nor static. Problems can arise in all the previous steps. Therefore, you must ensure the involvement of all your employees, at all hierarchical levels, in the continuous improvement of the process.
There are different techniques to promote continuous improvement. For example, each team can hold a daily meeting to discuss what has been done, what remains to be done, and potential obstacles. It’s a simple way to improve the process daily.
The advantages of lean management
The growing popularity of lean principles comes from the fact that they focus on improving every aspect of a work process and that they involve all hierarchical levels of a company.
Managers can take advantage of a few major benefits.
Concentration. By applying lean principles, you can reduce waste in your operations. Therefore, your workforce will focus on those that add value.
Improved productivity and efficiency. When employees are focused on delivering value, they are more productive and efficient because they are not distracted by unclear tasks.
Smarter process (flow regulation method). By implementing a method of regulating the flow, you will be able to provide work only when there is a real demand. This leads to the following advantage.
Better use of resources. When your production is based on effective demand, you will be able to use only the necessary resources.
Thus, your company (team) will be much more flexible and able to respond much more quickly to customer requirements. Ultimately, the principles of lean management will allow you to create a stable production system with a greater chance of improving overall performance.